POLYMER BASED DRUG DELIVERY
Polymer based dosage forms can be made using single screw and twin-screw extrusion technologies. An explanation of how extruders work and why they are customized will be given. Example process trains required to produce various shapes such as fibers, films, profiles, and coextruded shapes will be discussed. Lastly, case studies of polymer drug delivery dosage forms based on extrusion technologies will be discussed. One example of a case study will reveal the short-term safety and efficacy of a ketorolac loaded ureteral stent compared to a standard stent. In another case study, the distribution of clonidine after transforaminal placement of a biodegradable drug delivery depot system will be reviewed.
Polymeric based drug delivery dosage forms deliver drugs through one of two mechanisms: Diffusion or Erosion. A graphical description of the Diffusion Controlled and Erodible Matrix mechanisms is shown. Diffusion Controlled drug delivery involves the diffusion of the drug through a polymer matrix over time. Through this process the polymer remains intact while the drug is gradually deployed to the therapeutic site. This can be achieved either by encapsulating the drug in a polymer shell or coating, or distributing the drug throughout a non-degradable, or biodurable, polymer matrix. Erodible Matrix Implants are produced through the encapsulation or distribution of the drug in an erodible polymer, such as a water soluble or bioresorbable polymer. As the polymer erodes in the body, the drug is released. Dosage forms can be produced using twin and single screw extrusion techniques. Mixing occurs in both extrusion techniques although twin screw extruder’s primary function is to enable mixing and single screw extruders are primarily designed for pumping and shaping.
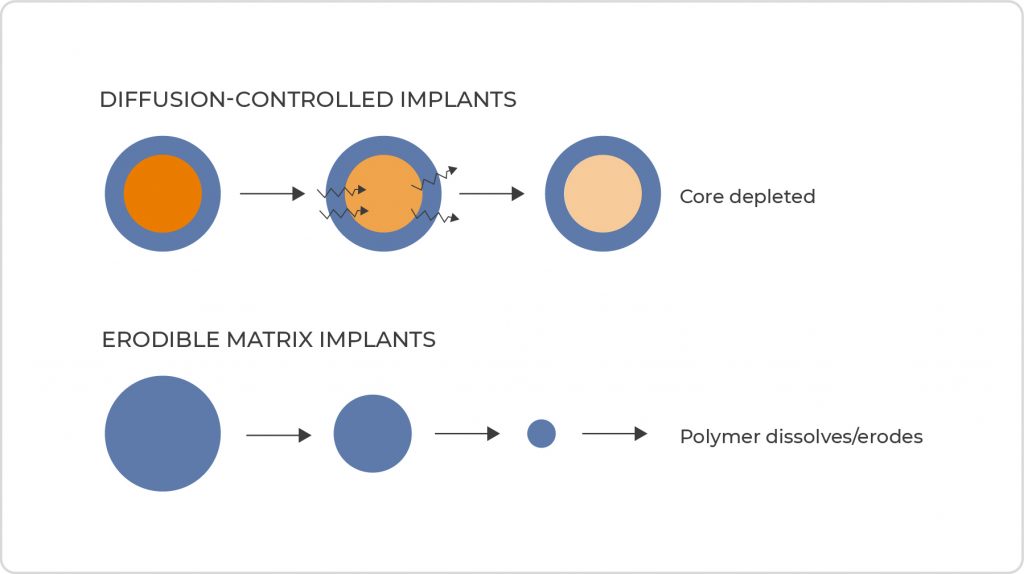
- Figure 1. Process flow of considerations to determine the proper regulation for DDCs.
Mixing is a key element in polymer processing. Mixing can be classified as being either distributive or dispersive. Dispersive mixing refers to the reduction of the size of the particles as well as the randomization of their positions in a polymer matrix. Distributive mixing, on the other hand, refers to the method by which the randomness of the spatial distribution of the API particles is increased without reducing their size (17).
Hot melt extrusion via a twin screw extruder as a continuous mixing device can offer several advantages including higher outputs, lower energy requirements, greater versatility, closer control of shear and temperature, and it is less labor intensive than batch mixers. Although the capital cost is more, the operating cost is less since compounding by this technique is a continuous operation.
The screws are assembled with segments which slide onto their respective shafts forming two screws which rotate side by side. The segments vary in design so that conveying, compression, melting, mixing or devolitilization can be controlled in the process. There are several different methods of operation with a twin screw. The extruder can be either co-rotating or counter-rotating, and the screw flights can either be non-intermeshing, partially intermeshing, or fully intermeshing.
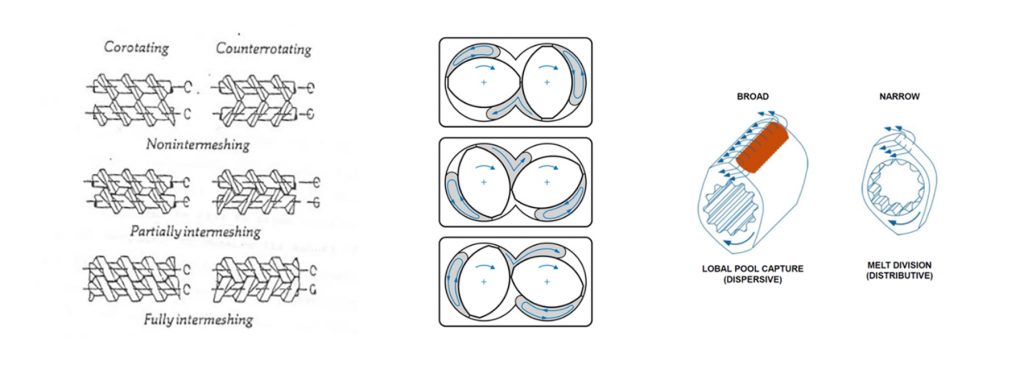
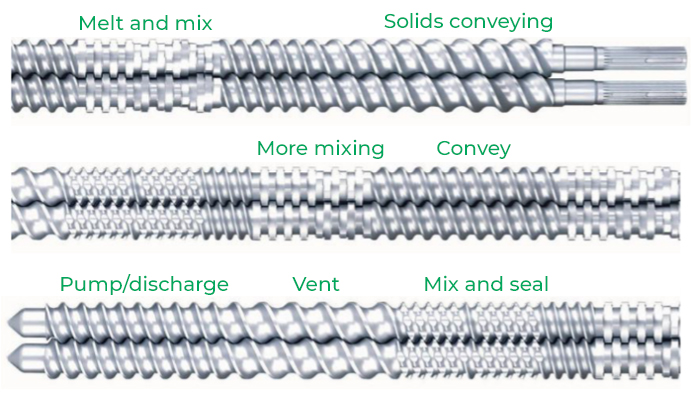
- Clockwise, from top left, Twin screw extruder modes, flow path in an intermeshing corotating TSE, kneading block examples, and process steps in a TSE.
Co-rotating, intermeshing screws mix the material in such a way that it travels a figure eight path around the two screws. These are known as self-wiping screws because the geometry of the two screws is configured in such a fashion that the root of one screw is constantly being wiped by the flight of the opposite screw. Counter-rotating, intermeshing screws function similarly to that of a two roll mill in that they depend on the clearance between the screws (analogous to the nip on a two roll mill) for the amount of mixing. Fully intermeshing, co-rotating twin screw extruders are the most commonly used twin screw extruders because of their ease of use and they are higher throughput machines. The elements and barrel sections are modular and can be selected to perform specific functions. Kneading blocks that are wide are more dispersive than narrow blocks that are more distributive. Pitched elements are used for conveying the material and the rate of conveying is dictated by the pitch of the screw. The smaller the pitch, the more turns around the screw and thus, the more residence time in the machine, and vice-versa.
Single Screw extruders are multifunctional machines in which solids transport, polymer melting, and pumping of the polymer formulation takes place. The geometry of a conventional screw for a single screw extruder as well as a functional diagram of its operation are illustrated to the left. In zone 1, solid state pellets are conveyed; compression and melting occurs in zone 2 where the polymer exists as a mixture of solid particles and molten polymer; and in zone 3 the polymer is completely melted and therefore exists as a fluid.
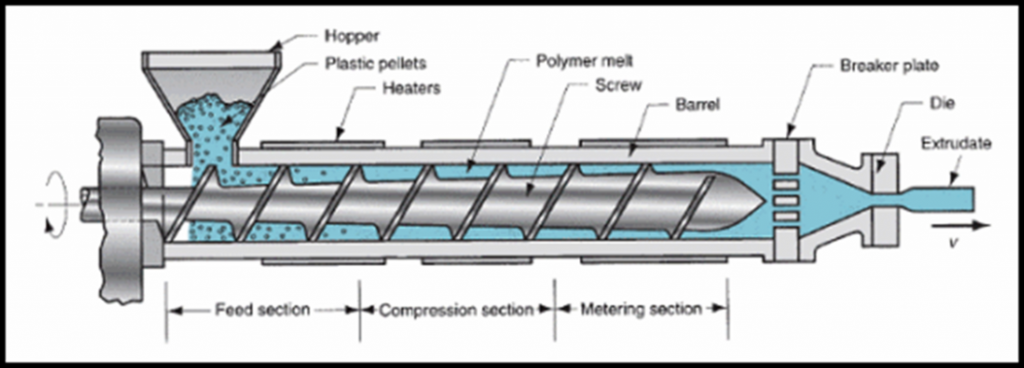
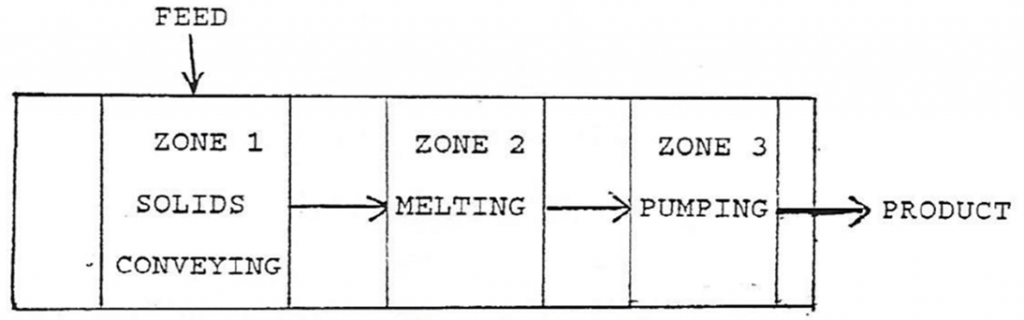
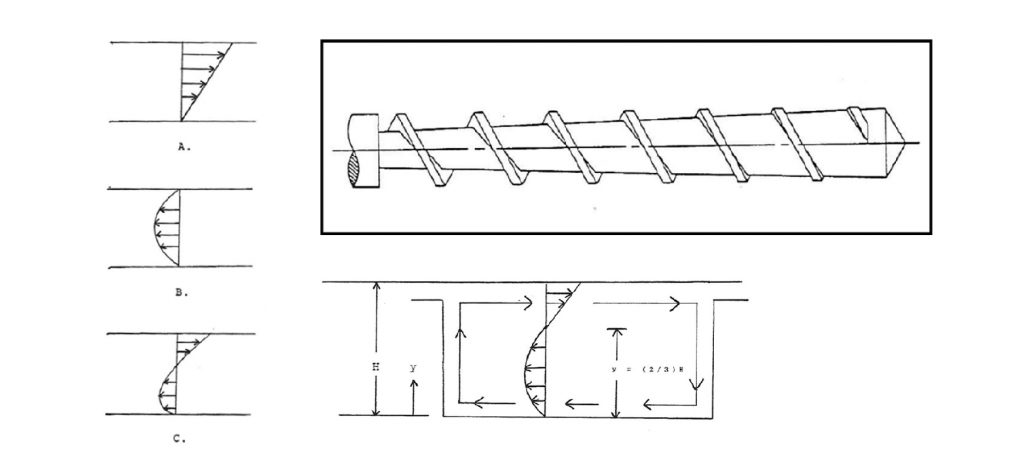
- Velocity gradients in the down channel (left) and cross channel (above) flow directions in a single screw extruder screw channel.
- A. Drag Flow, B. Pressure Flow and C. Resultant Flow
The relative motion between the screw and the barrel wall in the down channel direction produces a linear velocity gradient known as drag flow, the dominating flow in extrusion. The die attached to the end of the extruder exerts pressure on the molten polymer producing a negative flow opposite the direction of drag flow. As the pressure at the die end increases, molten polymer flows backward in the screw channel producing a parabolic velocity profile (pressure flow). At the clearance between the screw flight and the barrel, there is another flow loss, leakage flow. The amount of leakage flow is minimal and its effect is usually coupled with pressure flow. The resulting velocity profile, is the sum of these flows. A breaker plate is added to the machine after exiting the extruder barrel and before entering the die to orient the flow of the polymer in the die, mitigating the multiple flow directions experienced in the screw channel.
Polymers that are used in shape extrusion of drug delivery implants and devices consist of bioresorbable and biodurable polymers. Examples of Bioresorbable polymers include polylactic acid (PLA), polyglycolic acid (PGA), polycaprolactone (PCL), polydiaxanone (PDO) and various copolymers. Biodurable polymers are used to produce Diffusion Controlled Implants. Biodurable polymers include low density polyethylene (LDPE), ethylene co-vinyl acetate (EVA, at various VA levels), and polyurethanes. The types of shapes that can be produced by extrusion include fibers, rods, pellets, tubes, sheets or films and profiles.
Case 1 Bioeresorbable Drug Loaded Pellet
An example of a drug loaded pellet is reported by Beall, et al. Pellets were comprised of clonidine hydrochloride (HCL) and PLA to form a dose of approximately 300 micrograms. In vitro elution was carried out by placing three clonidine HCL loaded pellets in 2 ml of a phosphate-buffered saline solution (ph 7.4) at 37°C. Cumulative drug elution was plotted as a function of time. Sustained release of clonidine HCL was observed over 98 days. Elution of 56% of the drug was released in the 1st 28 days followed by a much slower drug release (29% of clonidine HCL) over the remainder of the test.
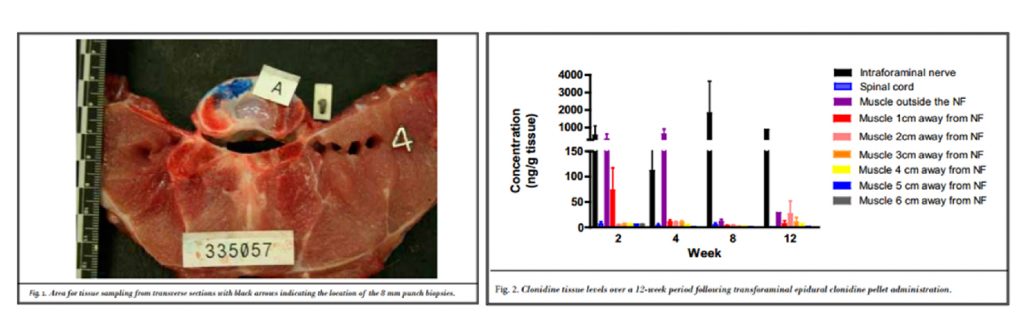
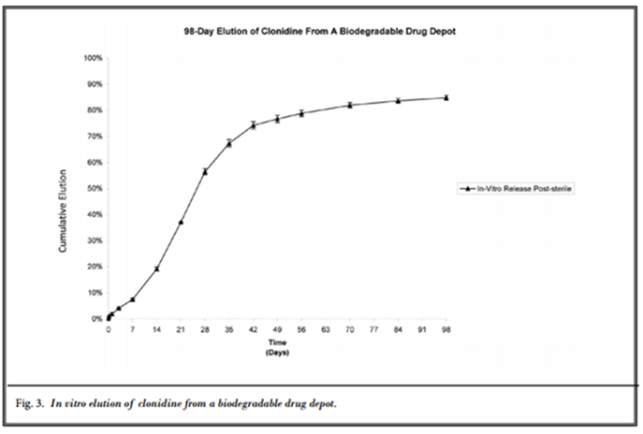
- Reference: Beall, D.P., Deer, T.R, Wilsey, J.T., Walsh, A.J.L., Block, J.H., McKay, W.F., Zanella, J.M. (2012). Tissue Distribution of Clonidine Following Intraforanimal Implantaion of Biodegradable Pellets: Potential Alternative to Epidural Steroid Injections for Radiculopathy . Pain Physician 2012; 15: E701-E710.
Case 2 Drug Eluting Ureteral Stent
Implantable and drug delivery tubes can be made from a wide range of biocompatible polymers to meet specific application requirements. Krambeck, et al, reported the results of a clinical study performed on patients using a tube extruded from a keterolac loaded EVA formulation and then converted into a ureteral stent. The polymer formulation comprises 13% ketorolac in an EVA polymer matrix. Ureteral stents are used to maintain urinary flow to the bladder after uretoscopy. The procedure is quite painful and the idea is to incorporate ketorolac as a pain medication to be delivered locally.
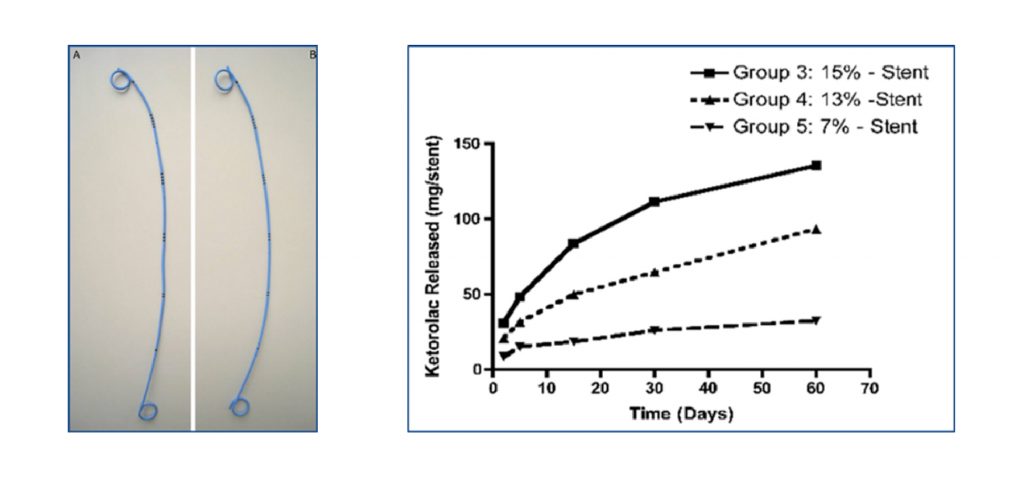
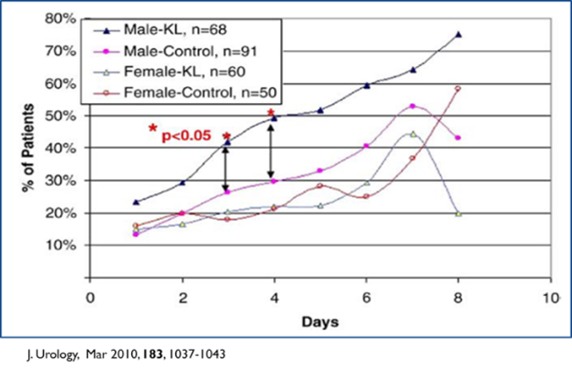
- Reference: Krambeck, A.E., Walsh, R.S, Denstadt, J.D., Preminger, G.M., Li, J., Evans, J.C., Lingeman, J.E. (2010) . A Novel Drug Ureteral Stent: A Prospective, Randomized, Multicenter Clinical Trial to Evaluate the Safety and Effectiveness of a Ketorolac Loaded Ureteral Stent . The Journal of Urology, Vol. 183, 1037-1043.
SUMMARY
- Polymer based drug delivery dosage forms are either Diffusion Controlled or Erosion Matrix. Distributive and Dispersive Mixing is critical in either dosage form.
- Twin Screw Extrusion is a continuous mixing process that is modular which can be designed to accomplish both distributive and dispersive mixing.
- Single Screw Extruders are multifunctional devices that accomplish pumping of a molten polymer formulation that is capable of producing precise dosage forms including fibers, rods, pellets, tubes, sheets or films and profile shapes.
- Two case studies are shown, one involving a bioresorbable pellet and another a drug eluting ureteral stent.
ADDiTIONAL REFERENCES
1) McKelvey, J. (1962), Polymer Processing, John Wiley and Sons, Incorporated, New York, New York
2) Middleman, S. (1977), Fundamentals of Polymer Processing, McGraw Hill Book Company, New York, New York
3) Hold (1987), Polymer Processing: An Overview, Chemical Engineering Progress
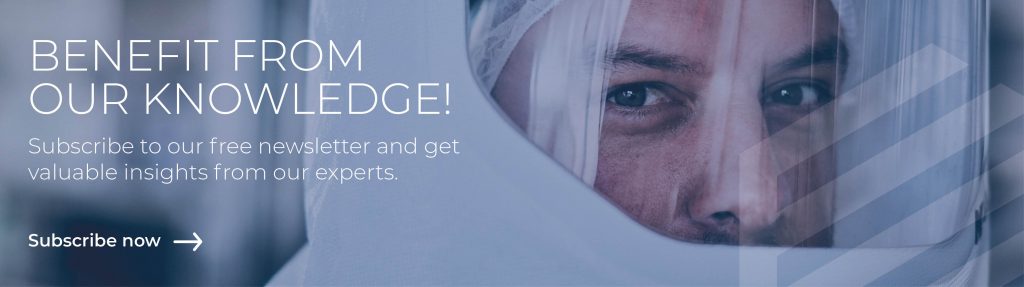