Hot Melt Extrusion and Solubilization
Approximately 90% of active pharmaceutical ingredients (APIs) in development are estimated to be poorly water-soluble (PWS)1. Hot Melt Extrusion (HME) is one of several solubilization techniques used by the pharmaceutical industry to enhance the solubility of APIs. HME is a desirable strategy because it is a controllable process that promotes miscibility of the API in a polymer matrix, it is a continuous manufacturing process that takes up a relatively small footprint, and it is solvent-free and scale-able.
Class I – High Permeability, High Solubility
Class II – High Permeability, Low Solubility
Class III – Low Permeability, High Solubility
Class IV – Low Permeability, Low Solubility
HME technology can be used to address BCS Class II molecules by improving the dissolution rate of PWS drugs to enhance their bioavailability after oral administration. These crystalline hydrophobic drugs are dispersed in hydrophilic polymers using HME to create amorphous solid dispersions.
APIs are commonly characterized using the Biopharmaceutics Classification System (BCS). The BCS system consists of the following four classes:
Formulation development involves the development of an API-polymer mixture that provides the desired release characteristics. Drug release is evaluated in-vitro by performing a dissolution test.
The scale of development is from mg quantities evaluated on a hot stage microscope and/or a differential scanning calorimeter (DSC). Small-scale studies can be performed using a vacuum compression molding (VCM) technique at a different time and temperature conditions. VCM studies are also conducted at the mg scale. Pre-clinical extrusion studies are typically performed at the 20-30g scale. The scale for clinical studies can be in the 100g batch size. Commercial manufacturing of GMP batches is in the 10s of kgs/hr range.
The benefits of twin screw extrusion
Although relatively new to the pharmaceutical industry, melt extrusion is a widely used technology in the plastics industry and has been for several decades. The extrusion process allows for either split feeding or pre-blending of the API and other excipients into the feed throat of the extruder. The extrusion process is very modular. The most common type of extruder used in HME to create amorphous solid solutions is a co-rotating twin screw extruder. Rotating screws impart shear and energy into materials being processed to facilitate mass transfer operations which means fewer process steps, the absence of solvents, and lower manufacturing costs.
The twin screw extruder is very flexible. The barrels and screws are modular and can be programmed to achieve the desired mixing required for a given formulation. Developing a screw and barrel configuration designed for a specific formulation is common. The barrels are unique and may be solid or vented. A vented barrel is open, which makes it possible to apply a vacuum to the solution.
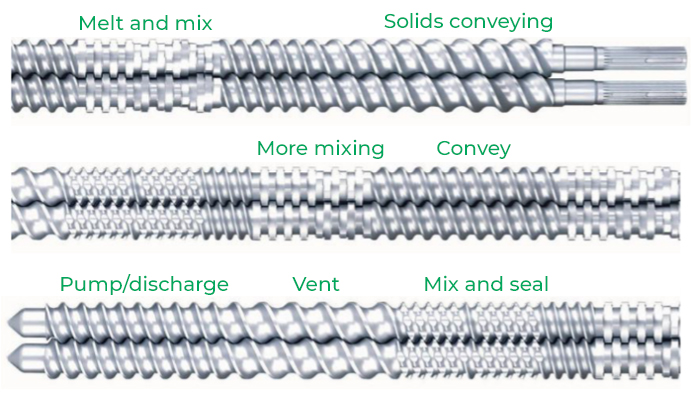
A continuous process sequence
Mixing in a twin screw extruder can be either distributed or dispersive. Distributed mixing is when there is a spatial distribution of components in the formulation. Dispersive mixing is when individual components are dispersed in the formulation. Dispersive mixing involves reducing the size of the components.
Screw elements can be flighted to convey material in different ways. Sometimes you want the material to move fast and sometimes more slowly to give it time to absorb the drug. Longer-pitched, flighted elements move the material down the barrel faster than shorter-pitched elements. Mixing different screw elements makes it possible to create one continuous process sequence, including melt & mix, solids conveying, pump & discharge, and mix & seal.
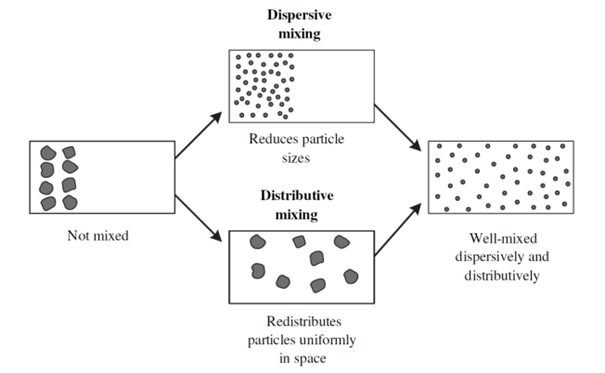
Solid molecular dispersions are achieved by a melt blending process, in which the API is dispersed and/or dissolved into a polymeric matrix. The resultant solid dispersion is extruded into a film or cooled strand and cut into a pelletized or granular form. Then granules are milled and blended in a tablet formulation, compressed into tablets, or filled into capsules.
Pictures published courtesy of Leistritz Extrusion Technology.
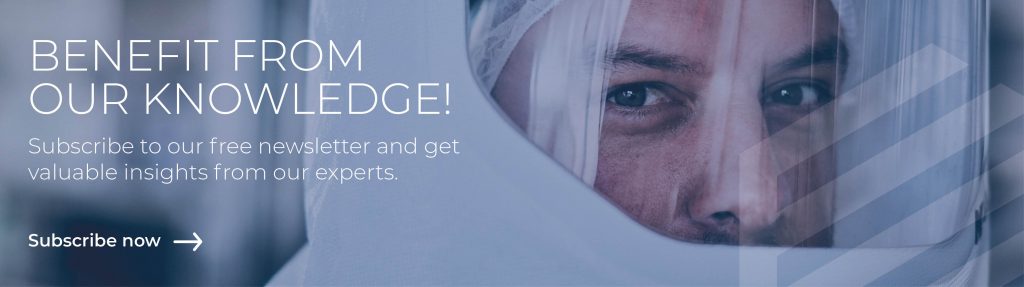